X70管道B型套筒自动焊工艺研究
来源:《管道保护》2023年第3期 作者:胡多多 时间:2023-6-21 阅读:
胡多多
国家管网集团东部储运公司抢维修中心
摘要:近年来,效率高、质量稳定的全自动焊接技术在长输管道施工中得到了广泛应用。针对X70高钢级大口径管道B型套筒自动焊接工艺开展焊接试验研究,选择全位置自动焊接系统,确定了B型套筒纵焊缝焊接、环角焊缝焊接等关键工序的自动焊接工艺,介绍了自动焊接注意事项及焊接缺陷的产生及处理方法,通过焊接试验表明焊接质量合格。将其与人工焊接进行对比,结果显示可以缩短焊接用时34%、节省耗材25%。
关键词:高钢级大口径管道;B型套筒;自动焊接工艺;焊接应用试验
长输管道自动焊技术具有效率高、质量稳定、对操作人员要求低的特点,目前得到了广泛应用,我国在西气东输三线、陕京三线、陕京四线、中俄原油管道二线等新建长输管道施工中也相继应用了全自动焊接工艺。本文选择管道外挂式全位置自动焊接系统,针对X70高钢级大口径管道B型套筒自动焊接工艺开展试验研究,为提升管道抢维修技术实力提供支撑。
1 单焊炬自动焊接工艺
1.1 B型套筒纵焊缝焊接
(1)坡口形式、焊接层次及道数。纵焊缝坡口形式为V型,背垫材质及规格为20号钢、3 mm×30 mm (图 1- a),其中坡口面角度β20.0 °±1.5 °, 钝边ρ0 mm, 对口间隙b2.5 mm~ 4.0 mm;错边量不超过3.0 mm,余高0 mm~2.0 mm,局部不高于3.0 mm,盖面焊缝宽度为坡口上口每侧增宽0.5 mm~2.0 mm,焊接层数为根焊1 层、填充焊4层11道、盖面焊1 层5道(图 1- b)。
图 1 B型套筒纵焊缝焊接示意
(2)焊前准备。采用链条卡具组对口方式。坡口两侧25 mm打磨出金属光泽。选择火焰加热方式,预热宽度为坡口两侧大于75 mm,并在距管口25 mm 处均匀测量圆周上4点的温度。预热温度≥80℃,道间温度50℃~80℃。焊接电流为直流(DC)、正极性接法(DC+),熔滴过渡为颗粒过渡。自动焊接轨道宜安装在坡口下侧,距坡口尺寸调节一致,角摆方式。按照焊接工艺要求,准备焊材。
(3)焊接试验。在管径1016 mm、X70管道进行B型套筒纵焊缝焊接试验(图 2),焊接参数如表 1所示。
图 2 B型套筒纵焊缝焊接试验现场图
表 1 纵焊缝焊接参数表
1.2 B型套筒环角焊缝焊接
(1)组对、焊接层次及道数。环角焊缝组对如图 3(a)所示,接头形式采用环形搭接角焊缝,组对间隙不大于2.5 mm,焊脚尺寸40 mm×40 mm,焊接层次及道数如图 3(b)所示。
图 3 B型套筒环角焊缝焊接示意
(2)焊前准备。焊接前先将纵焊缝的引弧板和熄弧板切割掉,打磨至套袖完整状态。焊缝两侧25 mm打磨出金属光泽。电加热、感应加热或火焰加热方式均可,预热宽度为角焊缝两侧大于75 mm,并在距焊缝25 mm处均匀测量圆周上4点的温度。预热温度≥30℃,道间温度30℃~50℃。焊接电流、熔滴过渡形式同纵焊缝焊接。全自动环形轨道与B型套筒平行且距离一致,摆动方式为角摆。按照焊接工艺要求,准备焊材。
(3)垫层及回火焊道。按图图 3(b)标注1至4焊道焊接垫层,3道和4道之间焊接回火焊道,如图 3(b)所示第5焊道。
(4)封根焊道。垫层及回火焊道焊完后进行封根焊,如图 3(b)所示第6焊道。封根焊要保证套袖侧棱角完全融合。
(5)回火焊道。在盖面焊时,在最后一道焊缝处采用回火焊道工艺,焊后打磨距母材1 mm厚,且平整,如图 3(b)所示第20焊道。
(6)焊接试验。在管径1016 mm、X70管道进行B型套筒环角焊缝焊接试验(图 4),焊接参数如表 2所示。
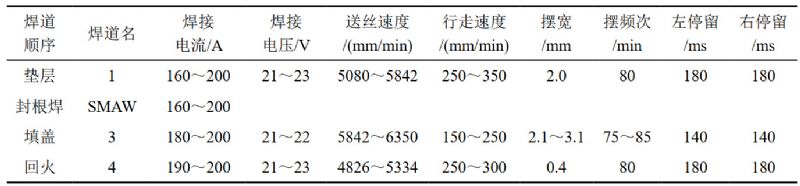
1.3 焊后保温缓冷
纵焊缝、环角焊缝焊接完成后,使用石棉被对焊缝保温缓冷(图 5)。
图 5 焊后采用石棉被保温缓冷
1.4 焊接质量检验
完成B型套筒焊接试验后,对焊缝进行质量检验。所有焊缝外观检查合格,48 h后采用磁粉探伤、相控阵进行无损检测,检测结果合格。
2 自动焊接注意事项
(1)安装纵焊缝焊接轨道时,检查磁性轨道吸力是否正常,有无消磁情况,轨道距离坡口边缘尺寸一致。环角焊缝轨道安装距离要保证从垫层到盖面依次焊接完成。
(2)开机前检查自动焊设备各个接头是否安装正确且连接牢固,开机后检查机头各个动作是否正常,检查气体流量是否合适。
(3)焊接起弧前应将焊枪调整至合适的位置,焊接开始就要调整焊枪与摆宽,观察坡口两侧的熔合情况。纵焊缝焊接时注意观察上坡口填充量及熔合情况,环角焊缝在打垫层焊接时控制好行走速度,在保证熔合正常的情况下尽可能行走快一点。每一层焊接完成后务必清理导电嘴,并调节保护气罩至合适位置。
(4)焊接工作结束后应将焊接小车从轨道摘下,放置小车前应尽量将焊枪送丝管捋顺,不宜打弯放置,否则易使焊枪送丝管变形,导致送丝不畅。
(5)每一层焊接完成后,及时清理层间飞溅,熔合不好的地方及时用砂轮机进行打磨至光滑过渡。在环角焊缝10点钟至2点钟位置特别注意层间及飞溅清理。
3 焊接缺陷的产生及处理方法
根据无损检测结果统计,焊接产生的缺陷主要有两种:圆形缺陷 、条形缺陷(含直线未熔及间断未熔)。
(1)圆形缺陷。形成原因: 焊口加热温度不够,层间温度不足;焊接时防风措施不到位;焊枪保护喷嘴清理不及时,保护气流量大或小都有可能会出现密集气孔;层间飞溅清理不及时。解决方法:清理好每层焊缝内的杂质,尽可能使用砂轮机打磨,清理时注意不要把焊道之间的搭接处打磨成夹沟;加强防风措施;将焊接电压略加大一些,从而减小飞溅程度,增强电弧的稳定性;加快焊接小车行走速度,角向摆动调节合适。
(2)条形缺陷。原因:焊枪的角度不合适,层间出现夹沟时未及时打磨平整,焊接电流过小。解决办法:焊接每一道时,调整好焊枪角度,熔宽搭接上一道焊缝的1/2左右,在焊接环角焊缝10点至2点钟位置时,容易出现较深的夹沟,应适当调节小车行走速度,减小摆宽,适当增加焊接电流。
4 效果对比
从所需工时、耗材两等方面对比自动焊接与人工焊接的差异,结果如表 3所示。
表 3 自动焊接与人工焊接所需工时与耗材对比结果
从表 3可以看出,不考虑轨道安装、小车调整、管口组对等用时及差异,与人工焊接相比,自动焊纯焊接用时缩短34%;采用药芯焊丝,比人工使用焊条节省耗材25%。焊工可由4人减至2人,其优越性突出。
5 结语
选择单焊炬全位置自动焊接系统,采用自动焊接工艺在X70大口径管道进行了B型套筒焊接试验,焊接质量合格。与人工焊接相比,用时短,耗材少,节省人力资源成本,经济效益明显。同时,自动焊接工艺降低了对人员技术水平的依赖。目前试验结果仅在车间进行了焊接试验,验证了采用自动焊接工艺焊接大口径管道B型套筒的可行性,没有模拟在役管道工况进行试验,取得的试验数据还有一定的局限性。下一步将结合在役管道封堵换管作业,在运行管道有一定压力和介质流动状况下,开展在役管道的自动焊接工艺研究,摸索出一套适用于生产实际的自动焊接工艺。
作者简介:胡多多,1992年生,硕士研究生,工程师,毕业于长江大学油气储运专业,现主要从事油气管道维抢修技术研究工作。联系方式:18552923260,hudd@pipechina.com.cn。
上篇:
下篇: