多模差动涡流内检测系统在油气田管道检测中的应用
来源:《管道保护》2024年第2期 作者:孙鹏 时间:2024-4-15 阅读:
孙鹏
四川德源管道科技股份有限公司
摘要:介绍了一种创新型的多模差动涡流内检测技术,该技术可以应用于非标发球装置、低压低流速等油气田小口径集输管道的内检测,为油气田管道的风险管控提供了新的解决方案。
关键词:低压低流速;小口径;内检测;多模差动涡流
目前部分油气田管道受低压低流速、变径管等因素制约,存在过盈量较大、椭圆形变、弯头曲率半径较大、非标收发球装置等复杂工况,容易发生卡球风险,影响管道内检测工作的正常开展。电磁涡流内检测器具有与常规皮碗清管器相似的机械结构,在保证检测器通过性良好的情况下,具备管道内腐蚀缺陷检测能力,为油气田集输管道检测提供了一种新的解决方案。
1 涡流内检测原理及特点
1.1 原理
电磁涡流检测是基于电磁感应原理的一种无损检测方法,其原理如图 1所示。首先,通过激励信号源产生标准的正弦交变电流通入检测探头的激励端,交变电流使得检测线圈周围产生变化的磁场,通常称该磁场为原磁场。变化的磁场又使得在待测导体内感应出电涡流信号。其次,导体中感应出的电涡流信号也会产生自己的磁场(通常称该磁场为感应磁场),涡流感应磁场同样会与线圈发生电磁感应作用,进而在线圈上感生电压。当导体中某些因素发生改变,如出现缺陷或电导率、磁导率、形状、尺寸发生变化时,将影响涡流的强度和分布,进而引起线圈感应电压的变化。通过测定线圈感应电压(阻抗)变化而实现无损检测的方法就是涡流检测。
图 1 涡流检测原理图
多模差动涡流内检测技术是在电磁涡流内检测的基础上,采用差动耦合的方式进行信号激励,并利用涡流检测对试件性能的多种参数作出反应,从而建立多种识别模型进行不同缺陷判别的内检测技术。
1.2 特点
多模差动涡流内检测技术因其高度集成化和类似于清管器的外形设计,以及优异的传感器性能,使得内检测器具有长度短、重量轻、通过性好、检测灵敏度高、检测速度快等特点,可以应用于低压低流速以及发球装置为清管阀管道的内检测。
2 多模差动涡流内检测系统
多模差动涡流内检测系统并非单指内检测设备,该系统由多模差动涡流内检测机器人、无源智能跟球仪、检测分析软件、智能跟球软件、用户检测数据管理系统以及内检测缺陷定位技术组成。该系统实现了从检测作业、检测器跟踪、信号分析、缺陷定位以及用户内检测数据管理的全流程管理,其中无源智能跟球仪和智能跟球软件组成了无源智能跟球系统。
2.1 多模差动涡流内检测器
多模差动涡流内检测器整体结构由驱动皮碗、里程轮系统、硬件系统和涡流传感器组成(图 2)。具有特点如下:
(1)与清管器外形类似的结构设计。外形尺寸与清管器类似,高度集成化,体积小巧、重量轻、长度短,收发球操作像清管一样简单,能够通过1.5 D弯头,可以使用标准发球筒、非标发球筒、清管阀、临时发球装置进行检测作业。
(2)大提离高灵敏度涡流探头配备大提离、高灵敏度低功耗涡流探头,能够快速、准确地检测出管道内部裂纹、腐蚀、金属损失、焊缝异常、针孔等异常缺陷。
(3)推动压差低至0.1 MPa。高度集成化的设计,使得检测器体积小巧、重量轻,低至0.1 MPa的推动压差即可完成检测器的运行。
(4)宽泛的检测速度范围。采用专利技术的高频采样探头,能够实现0.1 m/s~8 m/s范围内有效的、高质量的数据采集。
(5)对管道清洁度要求不高。专业研发的大提离、高灵敏度低功耗涡流探头对管道清洁度要求不高,检测前只需要1~2次清管,大大降低了检测前清管对管道生产的影响。
图 2 多模差动涡流内检测器结构示意图
2.2 无源智能跟球系统
无源智能跟球系统由无源跟球仪和智能跟球软件系统组成。
(1)无源智能跟球仪。该仪器的数据采集单元能够实现对通球过程中产生的多声源耦合声场及次声波阵列信号的采集,并上传至云端。其轻量化、高度集成、防水防尘、高灵敏度及高采样率的设计(图 3),使得无源智能跟球仪具有现场安装便捷、可靠性强、灵敏度高的特点;同时,它支持各种通讯技术的定制化开发,包括4G、5G、北斗、GPS、Nora网络等,以解决不同场景的应用需求。
图 3 无源智能跟球仪现场应用图
(2)智能跟球软件。智能跟球软件平台(图 4),整合震动次声信号处理算法以及云台后台数据处理模型,依托集成事件数据库,智能对清管器/检测器运行速度、位置等信息进行实时计算、预测及通报。具体功能包括:过球信号智能判别、检测器/清管器实时位置和速度计算与推动、跟踪记录及报告一键导出、地图应用以及与第三方系统对接等。
图 4 智能跟球软件平台界面图
3 现场应用
3.1 “阀发阀收”应用案例
被检测管道于2019年投运,收发球装置均为清管阀,管道规格为Φ168×6.3 mm,长度约2.9 km,设计压力为3.0 MPa,运行压力为1.65 MPa,日输送气量为2.8×104 m3/d~3.2×104 m3/d,输送介质为页岩气。
(1)检测面临的挑战。收发球装置空间受限,发球和收球均采用清管阀,常规检测器的电子硬件尺寸受限,因而无法采用常规检测器进行检测;工艺控制挑战大,采用清管阀收球时,由于没有足够的减速长度,检测器存在冲撞清管阀阀芯球筒的风险。
(2)解决方案。为应对上述挑战,根据收发球清管阀尺寸定制化设计和制造了PIGPROX电磁涡流检测器,并且与客户针对检测工艺进行了周密部署与安排。通过采用PIGPRO-TR无源智能跟球系统,在检测器进站前1 km进行工艺控制,降低检测运行速度,最终顺利完成检测,并获得了高质量的检测数据。
3.2 低压低流速原油管道内检测应用案例
被检测管道于2016年投运,线路上无阀室,收发球筒为标准球筒,管道长度28.45 km,管道规格Ф219 mm×6 mm。该线于2016年建成投产,设计压力2.5 MPa,发球压力0.65 MPa,收球压力0.52 MPa,输量范围是420~480 t/d,输送介质类型为含硫化氢原油。
(1)检测面临的挑战。介质中含有硫化氢,有较强的腐蚀性;运行压差约0.1 MPa,理论运行速度小于0.2 m/s,存在运行动力小,运行速度慢的情况,检测器运行时长约2天,对检测器长时间稳定运行提出挑战;监听难度大,速度慢,有保温层,且为沙地,信号不稳定,对监听器提出更高的挑战。
(2)解决方案。根据已发现的风险及挑战,通过双方讨论,为确保发球成功,发球采用以下解决方案:①搜集历史清管及检测信息,编写专项实施方案;②针对该管线进行结构设计,新增一节电池组(图 5、图 6),实测续航时间57 h 23 min,根据历史清管时长约51 h,满足管线检测要求;③采用公司自研灵敏度高,抗干扰能力强的PIGPRO-TR无源智能跟球设备。
图 5 长续航Φ 219mm电磁涡流内检测器设计图
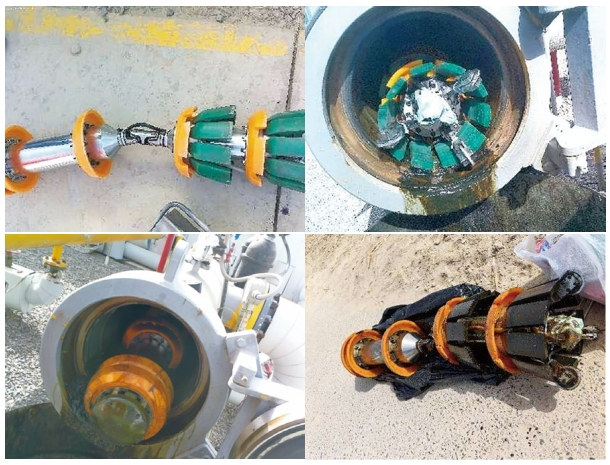
4 结语
多模差动涡流内检测系统在油气田管道的成功应用,填补了油气田低压低流速管道、发球装置为清管阀的管道以及不满足漏磁内检测条件的管道内检测空白,让原来“unpiggable”的管道变得“piggable”,消除了原来“unpiggable”的管道本体缺陷的管理盲区。同时PIGPRO-TR无源智能跟球技术与电磁涡流内检测技术的结合应用,突破了传统点式跟球的方式,实现了对检测器/清管器的实时跟踪与定位,为管道内检测作业安全运行提供了有力保障。
作者简介:孙鹏,1988年生,本科,高级工程师,国家一级注册建造师、NACE CP3、RT/UT/PT/MT/ECT/MFL等无损检测工程师,从事油气输送管道内检测技术与市场管理工作。联系方式:15708463536,sunpeng@deyuanpipe.com。
上篇:
下篇: